
SEWING & DRAFTING
Drafting: Dart manipulation

French Dart

Armhole Dart
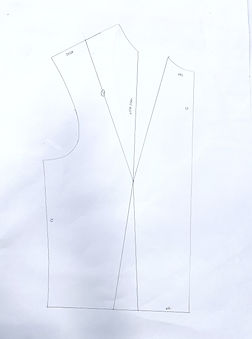
Neck Dart
Learning points:
Dart manipulation is the art of taking of existing darts in a sewing pattern, and manipulating them around the pattern to achieve something else. There were three types of dart manipulation we did in class: french dart, armhole dart and neck dart. I have always thought for manipulation of dart, you have to cut out manually to place the dart but i realised that it can be done by pivoting with a pencil and placing it correctly where I want the dart to end. The pivot method is when we move the pattern at the dart point, and trace around the pattern to remove or add fullness, instead of cutting into the pattern itself. The manipulation of darts is most fun and creative around the women's bust area, waist and neck. Personally, I am more comfortable with the pivotal method instead of the slash and spread method. However, pivoting a pattern is also a technique where there is more room for error, because sometimes the pencil will unknowingly move without noticing, and I end up with something unexpected for the result.
Drafting and sewing BLOUSE WITH PETER PAN COLLAR
Master Plan (Front, Back & sleeves)
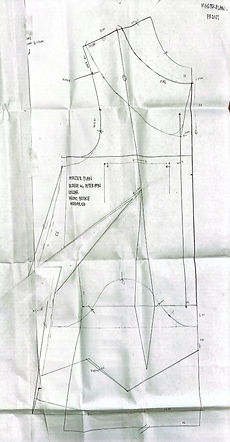
Front
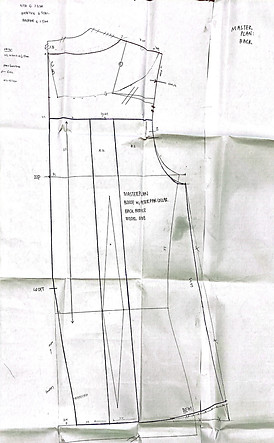
Back
For the front masterplan, there is a dart, a peter pan collar, a curved seam and zig-zag seam. There are notches applied on different locations so that they are matched accordingly when sewing. There is also a patch pocket on the front where we need drill holes so that its placed appropriately on the front. There are notches at the armhole as well for the sleeves to match. For the back masterplan, there is a yoke, pleat and godet. Changes were done with the appropriate measurements to get a new neckline as well as shoulder-line. For armhole and side seam, there was more allowance created for ease for the wearer.
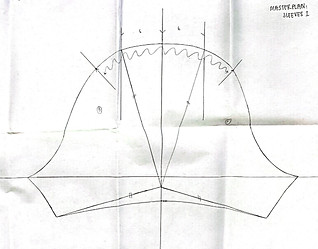
Puff sleeve
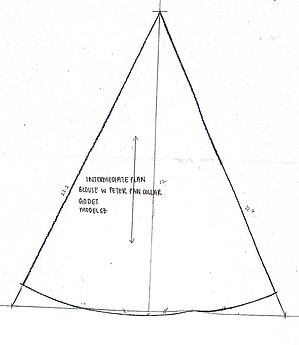
Masterplan of Godet

Plain sleeve
For the godet, both the diagonal lines should be equal and have a meeting point which is the centre point. The godet looks like a triangle but the bottom line we need to curve it out using curve ruler.
For the sleeves masterplan, there are two types of sleeves: puff sleeves and plain sleeve. The puff sleeve was more challenging because we had to cut out and place it on the paper with space for the gathers. The gathers have to be measured accordingly matching with measurements from the armhole. For the gathers we had to double the amount to ensure there is enough gathers. For the puff sleeve the hem allowance is 1cm instead of 4cm hem allowance on the plain sleeve as it is a curve hem seam. For the plain sleeve it was easier, we had to mark the back and front measurement of the armhole on the front and back master plan on the master plan of the sleeve. When cutting the hem for the plain sleeve, we need to fold up twice so there would not be a shortage of fabric to sew on.
Learning points:
Drafting the master plan was difficult because this blouse is very complex with style lines, different types of sleeves, collars and the back details. However, step by step with the guidance of the lecturers, I was able to draft and the measurements have to be exact while doing it so that when sewing up the garments there would not be any problem.
Intermediate plan
Learning points:
Intermediate patterns were easier to draft because we have already drafted the master plans. To avoid any mistakes, we need to ensure that we traced out the master plan properly and accordingly. Especially for the collars the shoulder line should match and the godet should match properly at the back as well.

Pleats

Final patterns
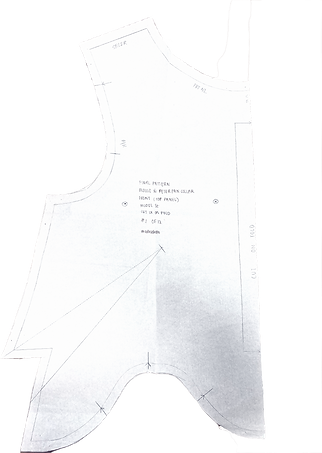
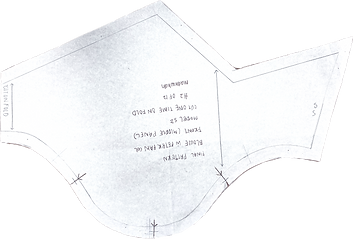

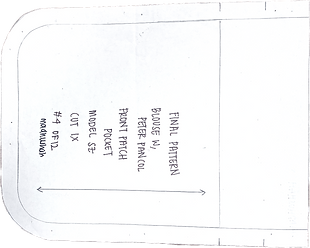
Top panel
Middle panel
Patch Pocket

Curve shape collar
Sharp collar
For the pleats, we first has to measure the appropriate measurements and fold the paper to form the pleats. The shaded part is where the pleat folds. It also has to be accurately traced from the back. For the collar, we need to draft two types of collar one with a sharp edge and one with curve-edged collar. We need to trace the collar from the front of the masterplan as well as following the back of the master plan. To check if your collar is correct, when placed on the masterplan the meeting point of the back and front which is the shoulder line should match.

Garment Construction:







Bottom panel
Sharp-edge collar
Curve-edge collar
Godet
Pleats
Yoke
Plain sleeve
Puff sleeve
Wearer's left back


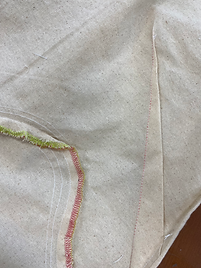
Sewing up the darts, first panel with curved panel and curved panel with sharp panel together. After sewing the curve seam and the zig-zag seam, we have to overlock them and it was challenging because I had to be mindful to not cut the fabric and i have to do it at a slow speed. Finish it up with decorative top stitches at the curve line and sharp straight lines

For the patch pocket before attaching it to the front, I had to do some long stitches at the bottom so that it nicely curved at the curve edges. After that I ironed out the folds and stitched it together with the front by sewing it carefully at the edge, it has to match the drill holes as well. I also folded the top parts of the pocket sides to hide the fraying.

Stitching the yoke to the pleats with a 1cm seam allowance.
Before stitching together with the yoke, carefully fold the pleats and ensure that the folded length matches with the yoke.

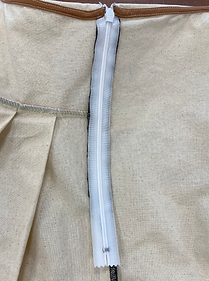
For this blouse, we did a concealed zipper. I attached it to the wearer's left first, from top to the notch position where it supposed to end. When approaching the plastic zipper stopper, I hand wheeled it to not spoil the zipper stopper. Then using a chalk i transferred the end point of the zipper to the other side and started sewing the other side of the zipper from bottom to top. I have to ensure that when zipped up the blouse is at equal length and its even.

Finished zipper look.
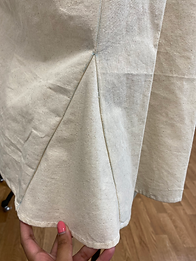
For the godet hem, I sew a line of large stitch 0.5cm from the edge and then fold up 0.5cm twice sew it at the hemline. After sewing the hemline, I attached the godet to the back and match it properly to the meeting point at where the notch is marked for the godet.


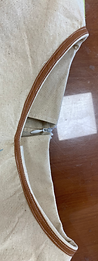
Bias Tape
Sharp-edge collar
Curve-edge collar
The collar was challenging because they were not identical collars one was curve while one was sharp. The part where I kept making mistake was the part when needed to fuse the interfacing and ensure that when it is placed on the bodice its on the bottom collar instead of the top. The purpose of the interfacing is to provides support, rigidness, and strength. I sewed the collar following the 1cm seam allowance and then snip it leaving 0.5cm for the collar, then flip it inside out and ensure that the interfacing is inside and should not be seen to wearer. After fusing the interface, we had to attach the bias tape and sew the neckline from front to back. Bias tape is commonly used to finish a garment, I had difficulties sewing it because the allowance to sew the bias tape is really small.

Puff sleeve

Plain sleeve
Before sewing the sleeves to the blouse, we have to prepare the sleeves. For the plain sleeve, we need some long stitch to form a little bit of gather to get the shape of the sleeve. Then, sew it by matching the notch points on the sleeve to the armhole. I sewed it with 1cm seam allowance and for the hemline, fold 2cm twice upwards and then sew it at the edge.
​
For the puff sleeve, we have to sew two lines of long stitch to form the gathers, and then adjust it accordingly to the gather measurements at where it should stop. For the puff sleeve, we did a french seam for the underarm seam. As for the hemline since its a curved hem seam, the seam allowance was sewed by folding 0.5cm twice. To attach this to the armhole, it should also match all the notches.
​
It is really important to mark the notches in your patterns and fabrics as it will ease the process of sewing. Without the notches, the garment may look distorted as it is not matched accurately.
What are the two types of stitching learnt?
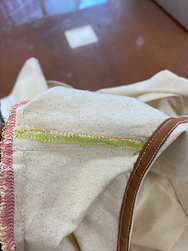
Plain seam
​
Plain seam was easy to sew as
compared to french seam we
had to sew by placing both
right side together and sew with a seam allowance of 1cm. Plain seam are usually found on T-shirts and blouses.

French seam
French seam was more challenging because of the very little allowance given, we need to place both the wrong side together to sew up with
0.3 cm seam allowance and then flip it over with right side together and sew up with seam allowance of 0.7cm. French seam usually used for lightweight and sheer fabrics such as silk and chiffon


Final garment reflection:
This is my final garment presentation. Overall, it was challenging as I had to go through a lot of unpicking during the process because I was not mindful of folds that is formed at the underside of the fabric especially curved and round seams. My most challenging part of the collar was sewing the bias tape and attaching the collar for the neck. I had a tough time visualising it and I kept sewing it wrong which resulted me in unpicking a lot. However, overall I am quite happy with the result because it turned out well and i was able to re-sew the parts i was not happy with. Through this process, I also realised how important is the accuracy of the paper patterns and notches. If the paper patterns are not accurate, during the sewing of the garment we will experience a lot of difficulties
PATTERN MAKING AND GARMENT CONSTRUCTION FOR MY FINAL SEMESTER PROJECT
For my final semester garment toile, I am making a denim dress and a denim vest as an outerwear. Since I am using calico for my toile, most of the details in my toile are a replication of denim jeans and garment. Here are my technical flats for your reference.


Denim dress construction
Pattern making : Masterplan Front and Back
Closing the shoulder dart
Moved the neckline 2cm in from the centre front and 1cm in from the shoulder
Formed the curved arch in the centre front according to the flats, I also needed to draft the facing for nicer finishing at the neckline. The facing was 5cm in from the original neckline
Marking the notch for the invisible zipper
drafting a curvier side seam towards the end for it to hug the wearer because i wanted it to be fitting for the wearer
Ensuring both denim waistband at the bottom of the dress are of equal length after the hem of the dress
Notch here to attach the side panel and centre panel
Notch here to attach the side panel and centre panel
Going in 0.5cm at the side seam so that it feels more fitted.
Length of the dress: 80cm
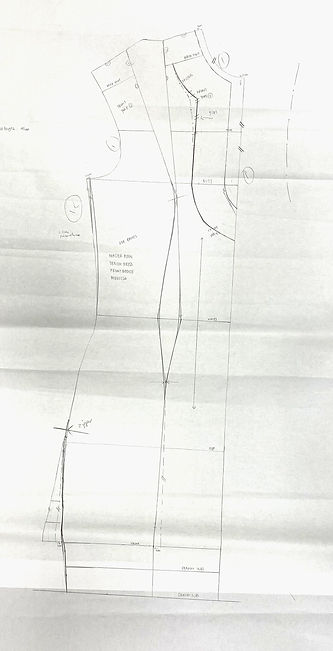
Front
Bringing down the neckline by 1cm and forming a facing for the back neck.
Notches to match the
side panel and the centre panel

Closing the shoulder dart and moving the dart towards the armhole
Armhole at side seam move in by 0.5cm
Notch for the zipper
Ensure that the side of the dress is not too straight and its for curved at the end for a nicer fitting dress for the wearer
Back
Drafting the masterplan for the dress was rather challenging at first because I was not sure and how to start and I was quite unsure how to move the darts in the dress. However, after consultation with my lecturer I was more sure on how to draft it and I realised it is quite straightforward. There were some parts which I found myself to redo quite a bit which was the length of the dress. I realised after completing both master plan the front and back were not matching in lengths which should be 80cm. Thus, I had to make sure they are both at 80cm and I had to do some correction here and there. The other part that was challenging for me was the two back yoke, there is already an original back yoke at the back but there is another two back yoke that comes to the front. Thus for this I need to put both drafts on top of each other to ensure that it matches. This will avoid any confusion during sewing.
Intermediate pattern for the back yoke

I had to do intermediate pattern for my back yoke cause on my master plan there are parts of the back yoke that comes to the front. Thus for my intermediate pattern I had to match the back yoke with the two other back yoke from the front to trace out my final pattern.
Final pattern for denim dress
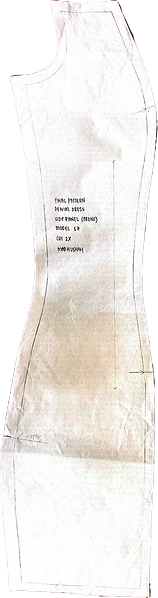
Side panel (Front)

Centre panel (Front)

Facing (Back)

Yoke (Front)

Back strip

Side panel (Back)

Centre panel (Back)

Facing (Front)
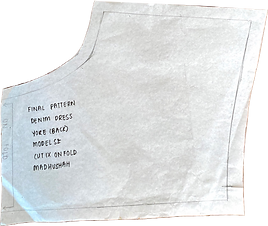
Yoke (Back)

Upper waistband

Lower waistband (interface)

Lower waistband (shell)
Belt loops
My final pattern for the denim dress was traced out from my master plan and my intermediate plans. I added the seam allowance for the final patterns, the seam allowance was mostly 1cm allowance except for the side seam and zipper area the allowance had to be 1.5cm.
Garment construction: Denim Dress


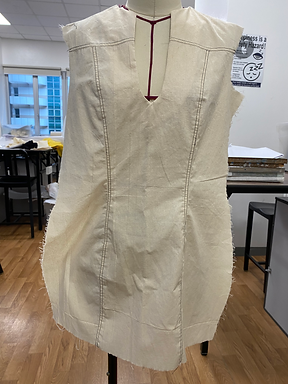
First I attached the side panel and the centre panels together. The centre panels are on fold so I had to attached the side panels together. When approaching the curvier sides, I had to be more careful when sewing them. After attaching the side panels, I did two rows of top stitching trying to replicate denim jeans stitching.

Top stitching
Then I attached the front two yokes of the dress and did another two rows of top stitching at the bottom of the yoke. I really like the two rows of top stitching because it really gives the feel of denim even though it is just calico.

Then I took a break from the front and moved to the back. As for the back I attached the centre back to the two side panels together with two rows of top stitching. The back strip was added on the centre back and edge stitch was done on the strip. Over here in the picture, I also pinned the back yoke.



The back strip is actually tucked into the back yoke so that it is not visible. Below the back yoke, I did two rows of top stitching as well. The final touch of the back which was my favourite is adding the belt loops to the back strip. For the belt loops I folded the strip 2cm by 2cm, sewed edge stitch on the strip and cut them into equal lengths for the belt loops. I matched them in the back strip and marked the point where I wanted to put the 'X'.
Front and Back together

After finishing the details on both the front and the back, I attached both the front and back by stitching the shoulder seam and over locking the seam. Then I moved on the facing. For the facing, it was a little challenging because there were a lot of round edges to sew. First i sewed the back facing to the front facing, then attached them to the front and back bodice. I was really afraid to overlock the edges of the facing because I did not want to cut any extra fabric while overlocking. At the end, I was quite happy that it fit perfectly.




Adding the zipper:
The zipper was the final touch before adding the waistband. I had to keep redoing the zipper because I realised i kept pinning them wrongly and they would not zip. I also made a mistake when I sewed the zipper at 1cm but on my final patterns i marked the seam allowance at 1.5cm. Thus, I had to unpick the zipper and sew it at 1.5cm. It was really frustrating at first but it started to work and the zipper worked perfectly.





Adding bias tape for the armhole for a cleaner finishing. For the finishing of the armhole, I had to press the edge along the seam line and sew close to the fold. Then,
top stitch in place with the right side (outside) of the garment facing you. This will ensure the stitching line looks neat even if there are variations in how you have pressed it. For my bias binding, it is a concealed binding so that it is not obvious for the right side.

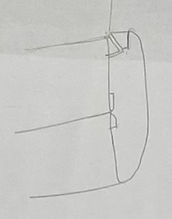
For the waistband, I sewed the two waistband in reference to the picture. I first attached the two waistband together with 1cm seam allowance and since the lower waistband final pattern was cut with double the size I folded it up to cover the stitching of the two waistband. Then I finished it by doing edge stitches on the waistband. I was also going to the add denim buttons on the centre of the waistband.

After prototype week, I realised that the dress was longer than I expected. I wanted it to be a mini dress, so I had to adjust the length of the dress by unpicking the waistband and cutting the hem of the dress. I shorten the dress by reducing 6cm.
Finished denim dress (toile) construction with details


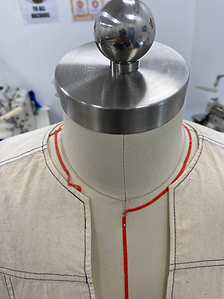

Shortened final length, I changed the stitching of the waistband to be at the centre point and dots to mark the denim button


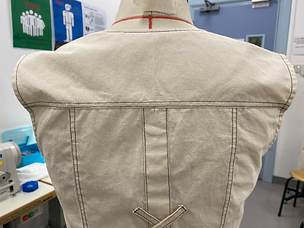

Front

Back


Denim vest pattern making & construction
Pattern making : Masterplan Front and Back
The length between the cut out was 7.5cm

Length of the vest: 100 cm
Removing the shoulder dart and
moving it towards the armhole.
This will help create a looser fit
and give me the intended silhouette I want which is a straight silhouette
Then I measured equally on where
I want my cut outs to be, but then I realise for it to have a proper drape both cut outs cannot be equal length, so the top one was 20cm while the bottom cut out was 17cm. The lines with the dots were the final cut out sizes.
The length between the side
seam to the first cut out was 3cm. It was a bit too dangerous to leave very little space between the armhole and the cut out but after draping it on the mannequin, it hanged properly, I decided to keep it at 3cm.
I brought the shoulder out by 5.5 cm and moved up by 2cm to have a more stiff shoulder and the adding of the shoulder pads. I also brought the armhole down for a loose fit at the armhole.
The neckline was moved by 2cm and at the shoulder moved in by 2cm
Waistband dept: 4.5cm
Front
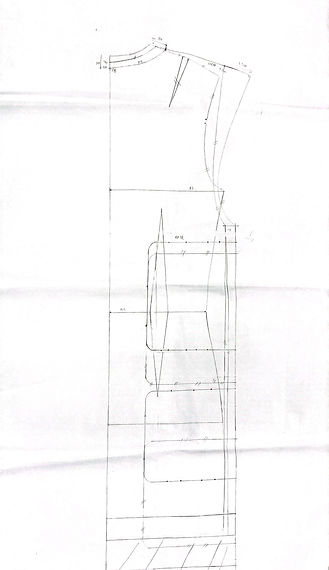
For my vest, the master plan is
pretty straightforward because both
front and back are symmetrical, therefore
the changes made in the front
should also be applied to the back.
My cut outs at the back should be
at equal lengths and match the front
because the cut out is a continuation
from front to back.
The dart at the shoulder was closed, to ensure a more straight silhouette
The neckline at the back is much higher as compared to the front.
Ensure that the waistband at
the back also have equal length
and dept as the front.
Back
For my vest, there was no intermediate patterns to be done, so I moved on to my final pattern.
Final pattern for denim vest

Front bodice with seam allowance of 1.5cm at shoulder, 1cm at neckline, 1.5cm centre front for zipper, 1.5cm at side seam and 1cm at hem
​
CUT 1X SHELL (CALICO)
CUT 1X LINING (COTTON)
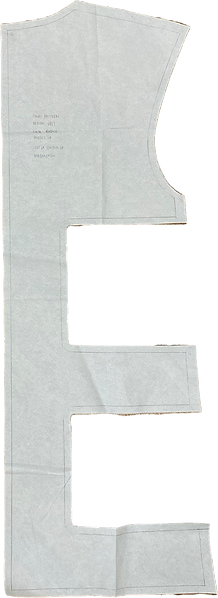
Back bodice with seam allowance of 1.5cm at shoulder, 1cm at neckline, 1.5cm centre front for zipper, 1.5cm at side seam and 1cm at hem
​
CUT 1X SHELL (CALICO)
CUT 1X LINING (COTTON)

Waistband for the bottom of the vest.
Double the waistband so that i can fold up during sewing. 1cm seam allowance for each side and to cut interfacing to fuse at the upper waistband. Interfacing will be cut according to one single waistband.

Belt loops
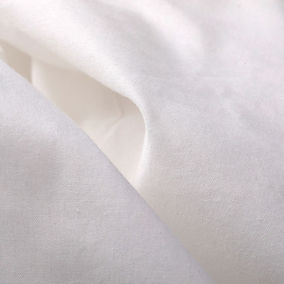
For the toile, I used poly-cotton fabric as my lining. This lining polyester is equipped with a nice sheen and shows to be a part transparent. The cotton gives the softness to the fabric whilst the polyester fibres add the crisp texture. It creases less and minimal ironing is required.

Standing Collar with centre front and centre back. It is important to mark notches at the shoulder line to match with the neckline while sewing.
Garment construction: Denim vest
Reflection:
Drafting and constructing two garments was really challenging for me especially when there were many tiny details that I had to add for both garments. I spent a long time trying to perfect my dress and when it was time to sew my vest, I was running on very tight schedule and was not able to complete the vest fully as compared to my peers. Thus I am still in the process of sewing my vest. After prototype week, I had to make a lot of changes to my vest, especially the length of the vest and how well it drapes and hang low. Thus, I had to redo my drafts and re-cut all my fabrics and linings and had to restart the sewing process for the vest. With the pressure of not being able to finish on time, I did not collectively take pictures of my development. However, I was able to annotate on what I did step by step.
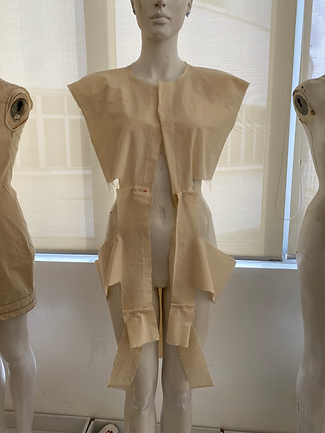
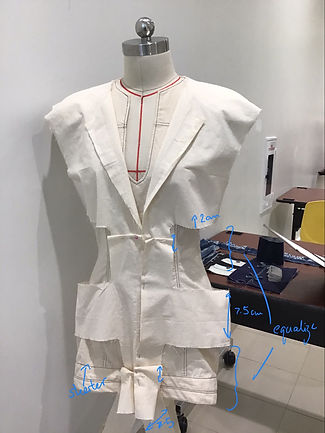
Prototype week changes
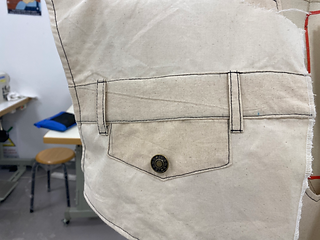


Firstly, I started off by doing the small details of my garment, in this case was the waistband replica, belt loops and a flap top pocket. For the waistband I iron on the interface to make it more stiffer and folded in 1cm, then I aligned the pocked at where I wanted it to be. The top seam allowance of the pocket should be aligned with the seam allowance of the waistband. When everything was properly place, I did edge stitch around the waistband and pocket. Then I attached the denim button on the pocket flap. After that was done, I measured equal lengths of where i want my belt loops to be placed. This whole detail here were inspirations from denim jacket and jeans.
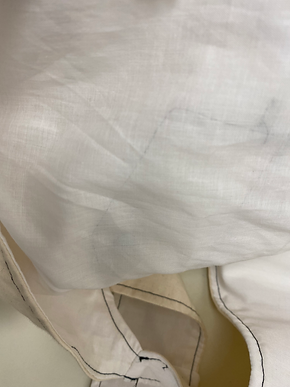

Before sewing the lining, I had to interface by front bodice and back bodice, to ensure that the fabric is stiff to hang and drape the intended way it was supposed to. After fusing the interface, I sewed the centre back together as well as the shoulder seams. For the centre back, I also did an edge stitch as decorative stitch to replicate denim jacket.
​
Then, I moved on to the lining. The trick is to always sew lining with lining and calico with calico. Since there are large cut outs in my garment it can be quite confusing and lost, it was also important that my garment does not twist while sewing. After sewing the lining, it lined perfectly with the calico. I had to also make sure that right side are facing each other before I sew.



The sewing of the side seams was something new that I learnt. With the cut outs, my side seams were mostly like panels so what we did was to put the back bodice and insert it into the front bodice through the opening. Flip it inside out and pull out the back and make sure it aligns with front seam and sew at 1.5cm allowance. When you flip it over to the right side, it is a clean finishing and all the raw seams are hidden inside the lining. You must also be sure to snip so that when flip out they are both of equal lengths.


After sewing the side seams, the lining was completely done. I had to reinforce the lining, by doing a 0.5cm top stitching around the cut outs and the armholes. Have to ensure that the cut out matches and is a continuation from front to back. Sewing the top stitching at the cut outs was quite challenging due to the sharp curved edges and since I am using a contrast colour thread, mistakes would be very obvious if not done properly. At times when the stitching is a bit off, I had to unpick and sew it again to ensure that the top stitching is curved nicely.
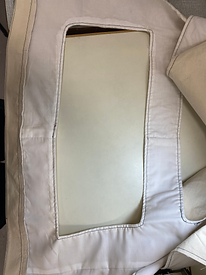

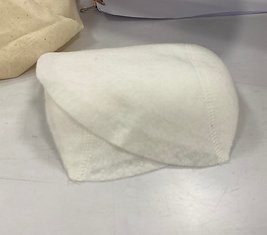
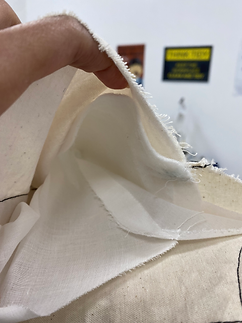
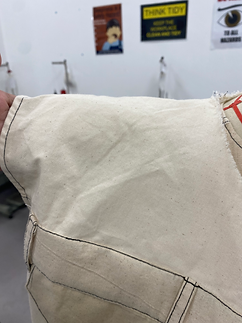
Adding shoulder pads to my shoulder seam by back tagging on the the ends of the shoulder pads. I folded the shoulder pad into half first and marked the centre points and placed the centre marking on the shoulder seam. Then I back tagged the on front and back of the shoulder pad to secure it. I had to do this before sewing the neckline and collar so that I can hide the shoulder pads inside my lining.
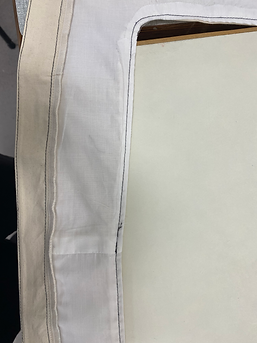


Adding the waistband:
First, I had to fuse the interface at the top of the waistband and then I fold the waistband into half. I attached the top of the waistband with the hem of the vest with 1cm seam allowance. Then i folded the bottom 1cm seam allowance and matched with the sewn seam so that it has a clean finishing. Then i top stitched the top and bottom of the waistband. I actually intended to put the belt loops on the waistband. However, when i pinned them it did not look as nice as I though it would be. It felt like it was a bit too much. But I am still considering, I might add it in when I am almost done with the garment.
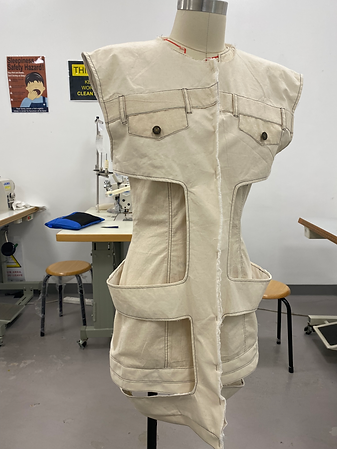
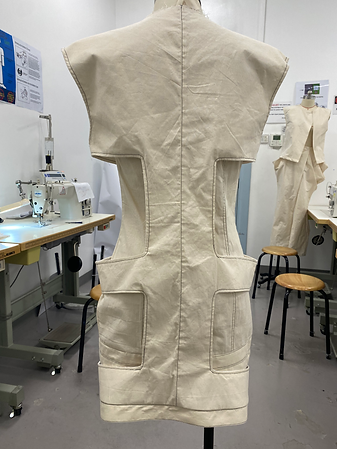
Current progress of front and back of the vest
Sewing a standing collar for my vest
For my collar, I am doing a standing collar and I was a little fearful of sewing it because I did not want to screw it up but then I realised the sewing methods to sew the collar was very similar to the waistband. So first I sewed the 2 pieces (calico & calico with interface) of collar together with right side facing each other leaving out the centre back and the centre front because I need to overlock them. Then after that I tag at some points of the neckline so that the calico and lining will be one piece. By tagging them, it will be easier to attach the collar so that it does not move. Then I attached the collar and just like the waist band the other side that is loose to fold in 1cm and match at the stitch line. Lastly, I finished the collar by top stitching the top and bottom.




Sewing open-ended zipper



Sewing the zipper was the last touch of the garment and it was really difficult for me. Mainly because the zipper was too long and I had to manually take out the zipper teeth to shorten it and put the zipper stopper near where I wanted to put it. I also altered where I wanted the zipper to start from which was above the waistband and I think it looked nicer that way.
For the zipper I sewed it 1.5cm in the centre front and then did a top stitch after at 0.5cm. I also needed to ensure that the top stitching was done neatly in straight line.
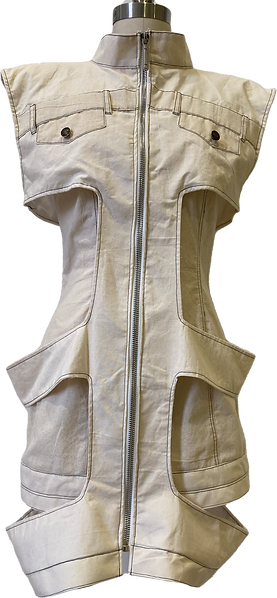
Front
Final
toile
display

Back


What have I learnt from sewing & drafting this semester?
Just like draping, sewing & drafting is something really new to me. Even though I did take short courses on sewing outside school, drafting a whole garment was difficult for me. I was not used to it and I needed constant guidance to ensure I am doing things the right away. For drafting and sewing, precision is very important especially with measurements, if its 1.5cm seam allowance it has to be sewed at 1.5cm allowance. I also realised that the paper patterns are really important to sew up a nice proportionate garment. If the patterns do not match and notches are not marked, the garments can look distorted and the efforts of sewing it will be a waste.